Concrete in Green Building
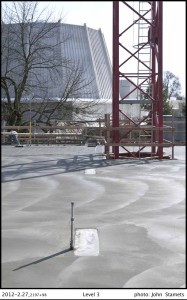
(C) John Stamets
Buildings are the most widespread and durable artifacts of modern society. They outlive their designers and builders and they continue to exert their influence on the environment long after they’re built.
Concrete is the foundation and frame of the construction industry; it’s what makes buildings last.
Ordinary concrete typically contains about 48% crushed stone, 34% sand, 6% water by weight, along with about 12 percent Portland cement, the glue that binds these material together. At about 11.5 billion tons per year, the concrete industry is one of the largest users of natural resources in the world.
Production of Portland cement is highly energy intensive, and depending upon where it’s produced, nearly a ton of CO2 is released into the atmosphere for every ton of Portland cement produced. It’s estimated that nearly 7% of global CO2 emissions are the result of Portland cement production. Its large volume and weight embody additional energy from transported materials to the plant and the finished product to the site. And the process of extracting, producing and placing concrete uses large amounts of fresh water.
So what is the appropriate role for concrete in a super-green, high-performance building?
There are a number of ways to mitigate the environmental impact of concrete. Fly ash, a by-product of coal generated electricity, or blast slag from steel manufacturing, can be used to displace up to 50% of the Portland cement in the concrete mixture. Recycled aggregates can reduce the energy required to mine and transport material, and grey water can be used instead of fresh water for the mixing, wash-water, and curing of the concrete.
To meet the Living Building Challenge, the materials in this category (Division 03 of CSI’s MasterFormat), must be sourced within a 500 km radius. The Portland cement used in the Bullitt Center comes from Delta, British Columbia, about 125 miles away. The sand and gravel are from a mine in Sumner, Washington, about 35 miles away. These materials are mixed at Cadman Concrete’s batch plants in Redmond (15 miles) or Issaquah (17 miles), then trucked in mixers to the building site, where the concrete is pumped or poured into footings, floors, walls, columns and decks.
Different parts of the building require different characteristics and strengths. Depending on the part, fly ash was used to displace up to 20% of the Portland cement, and in some cases, the admixture Hycrete was added as an additional waterproofing agent in places such as the exterior walls and the cistern, to extend the life of the concrete.
Concrete serves as the foundation and pedestal for the upper floors, whose skeleton is heavy timber and steel. Where the building meets the earth, concrete holds back the soil, keeps groundwater out, retains rainwater, and transfers the weight of the building to the ground, and is expected to deliver these services to the building for at least 250 years.
The un-reinforced concrete dome of the Pantheon has been in service for more than 2,000 years.
Because it absorbs and retains both warmth and “coolth” well, it is an important part of the building’s heating and cooling strategies. A four-inch concrete deck at each level, embedded with hydronic tubing that will circulate hot or cold water, depending on the season, will serve triple duty as the finished floor, the heating and cooling system, and additional structural strength for the building.
The environmental impacts of mining, manufacturing and transportation of concrete in this building have been minimized by using it purposefully for it’s strength, durability, and multi-purpose characteristics; sourcing it regionally to limit transportation energy; and displacing as much Portland cement as possible, while still achieving appropriate strengths.
Used thoughtfully, concrete has an important role to play in a building meant to last a long, long time.